Exclusive: This content has been pre-released from The Business Profile
In the face of both company-specific and industry-wide challenges, Atlantic Grupa has strived to stay one step ahead. They’ve done so with an emphasis on digital transformation and human resource optimisation; under the wider banner of ‘change management’.
Overseeing much of this effort has been Darija Pizent, the company’s Director of Supply chain Management. Here, she discusses why 2017 was such a pivotal year in changing the mindset of a decades-old organisation, to become more resilient and agile in the face of the big challenges we all know were yet to come.
Hi Darija. Please begin by introducing yourself and Atlantic Grupa, including a brief history and overview of the organisation.
Atlantic Grupa is a multinational manufacturing company and leading distributor of fast-moving consumer goods in the region of Southeast Europe. At present, we are made up of 17 distribution centres, more than 1,000 vehicles, and direct access to more than 70,000 sales points that offer comprehensive knowhow in areas of key account management, category management, logistics, and trade marketing.
Our journey began some 30 years ago as a distributor of chewing gum, but has since evolved to own a rich portfolio of food and beverage products, that are exported to more than 40 markets worldwide.
As a Director of the Supply Chain for the past five years, I have helped guide this ongoing growth by managing and leading all supply processes across the Croatian market.
Click Below: Read the brochure version of this content
Despite the substantial growth of Atlantic Grupa, nearly all organisations have found life tough in more recent times. During this critical period, what specific challenges have you faced, from an industry, geopolitical, or even company-specific perspective?
As a distributor with a strong and diverse distribution network, we’ve faced many challenges, like all organisations. Primarily, this has included a lack of labour in the operations segment, that has certainly worsened over the past five years.
There is also the local challenge of managing peaks. For example, in Croatia, we have a high summer season where our volume is at least doubled for some items, or can multiply by eight times compared to off-season rates for certain drinks and of course water. During those times, you can imagine the real pressure to meet demand from that aforementioned labour perspective – to ensure sufficient resources within the warehouse, drivers for distribution, and a top-up of seasonal workers to further meet that challenge.
Then comes the more collective issues we’ve all faced. Mainly, the sharp evolution of customer demand caused by the pandemic, that have been exacerbated by global supply challenges and availability of materials crises. This caused difficulties in managing ideal stock levels, to ensure availability without generating too much waste.
Having faced all of these challenges head on, we are now also preparing strategies to mitigate the impacts of inflation and a recession.
Throughout all of these trials, what steps have you taken to try and mitigate their impacts? Was it a case of protecting the processes and assets you already had, or did you take a more proactive approach to futureproofing the company?
Certainly, the latter. What made us successful in mitigating all those challenges was the team and support we had, not just in staying resilient, but in implementing a proactive digital transformation programme.
It was firstly imperative that we nurtured and retained a continuous improvement mindset regardless of the situations, complemented by a high-performing culture in our team. More generally, you could say this was a case of nurturing our change management credentials.
We created our continuous improvement strategy by finding the required support and using a test-and-try model in everything we wanted to implement. This began in 2017, where we set up a small team of specialists whose focus was to work on existing systems, to find inefficiencies in processes, and to measure all the details and steps taken in that current state. They would detect gaps and propose upgrades, new solutions and changes.
Before that, this wouldn’t have been possible from a time and effort perspective – we were too consumed with daily or seasonal operational challenges, meaning those gaps in the system and processes became even more significant as the business grew.
By focusing these continuous improvement efforts on the warehouse and transport operations especially, we could seek to find new efficiencies, while also gaining more control of logistics as a whole, ahead of what has proved to be a challenging time of change.
All of the above efforts came down to putting service levels and our customers as a priority, and that approach has opened up new opportunities as a result.
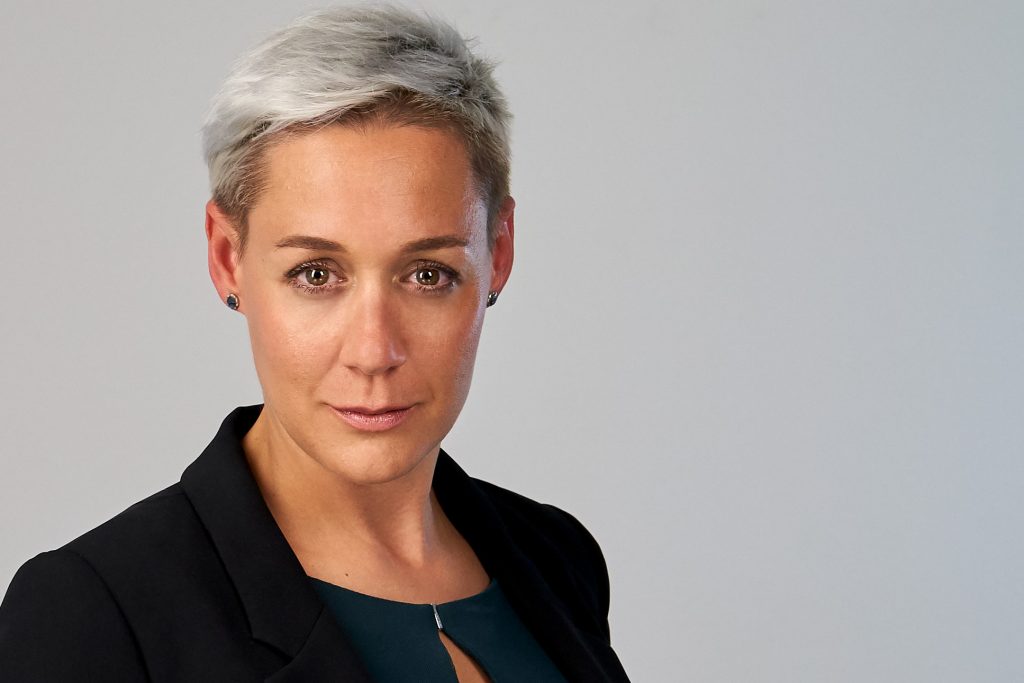
It is often said that digital transformation can’t be separated from change management – it seems that this ability to connect the two principles has been critical for Atlantic Grupa in recent years?
We in the supply chain strongly believe that new technologies can and will continue to play a significant role in assuring a competitive advantage, and therefore must be a strategic imperative as part of wider change initiatives.
Operational efficiency, a more transparent network to all stakeholders, and access to real-time information are all crucial to meeting challenges and market demands, off the back of this focus on digital progression.
And that’s why we embarked on our digital transformation journey back in 2017. We were building a new distribution centre, and at that point, we thought of this centre as a perfect hub for testing new technologies. Our first upgrade saw the implementation of a multi-picking process to enhance productivity. A cycle counting methodology also improves upon traditional, rigid methods of stock counts as they can be carried out during work hours throughout the year, rather than during a closedown period where we lose three days and three nights. In addition, we also sought to improve our connection with suppliers through new electronic data interchange (EDI) and yard management solutions.
One of the quickest-implemented projects with the highest productivity increase was the implementation of a voice picking solution. And the most intense project, which lasted more than a year, saw us introduce digital shipments for last-mile deliveries, which made the whole process from order, to delivery, and returns, more visible and paperless.
Ultimately, optimising change management was the most significant imperative for introducing new or innovative technologies in these early stages of the journey, and that has made this whole period successful. It was an initial effort that culminated in 2020 when we partnered with Croatian company, Gideon, a developer of AI and 3D-vision-based autonomous mobile robots for material handling in supply chain operations. This was a critical moment after three years of such proactive investment.
Content Sponsor: TESISQUARE
Since then, what have been the key projects that you feel epitomise this emphasis on digital transformation, and that are already showcasing the power of relationships with businesses like Gideon?
Our most defining moment more recently saw Atlantic Trade and Atlantic Grupa receive an Industrial Research and Innovation (IRI) grant from the Croatian Ministry of Economy and Sustainable Development. This was also awarded through the Agency for SMEs, Innovations and Investments which is co-financed by the European Union from the European Regional Development department.
The grant was targeted towards our work on the implementation of the project: Research and development of an intelligent modular management platform in the logistics process.
The project began on 17 August 2020, in cooperation with Gideon Brothers, as well as the Faculty of Mechanical Engineering and Naval Architecture. It will run until 17 August 2023, and during this period the project will receive a total contribution from the EU of 2.219.446,17 EUR (16.645.846,33 HRK). The total project value is estimated at 3.590.383,78 EUR (26.927.878,34 HRK).
The project’s general goal is to contribute to developing the logistics industry, to enable better business results for people in business, and to improve the quality of lives and availability of products for users around the world. This will be achieved by implementing research and development activities necessary for developing a modular platform for managing logistics processes. Achieving the goal will also enable the commercialisation of the project’s expected results, including modules of the mentioned platform and complementary consulting services that the applicant will be able to provide on the global market after implementing the planned activities.
From an internal perspective, the project team is working intensively on this research and the development of a modular platform that can allow us to integrate robots in the picking process. At the moment, we are entering the final phase and planning to put robots in real-life scenarios in warehouse operations as a result. This project will be a game-changer in many aspects, and I feel so much pride and excitement to be part of it.
At such an exciting time revolving around tech and innovation, how important is it to also include the human element too, and to foster a positive relationship between ‘man and machine’ throughout the digital transformation process?
I think that technology and digital intervention are changing how we work, produce and consume. However, it is not making the human element trivial or irrelevant. Rather, it’s making it more crucial than ever, and the sooner we accept that, the better!
Robots or any form of automation are not here to make workers irrelevant, but to make their work tasks more accessible and more efficient. For example, a picker will collect an ordered item and walk less if there are robots doing the movement aspect for them. Warehouse management experts will become robot specialists, but they must be given the chance to test and try each application, so they can learn and develop with each new innovation.
If you don’t provide an environment that includes development and knowledge of human resource, then those key skills will leave; or, even worse, stay, but you will lose the competitive advantage you were aiming for through the tech.
Speaking more about that company “environment”, please allude to the overarching culture you’re looking to create within the business.
Change management is imperative. If you are introducing robotics or any similar technologies, it’s not only the ROI of the project that matters. You have to calculate and talk about the return on investment of change management… of workforce adoption… of overall company use and optimisation. The implementation itself is never enough. That adoption and understanding process are what decides the overall success of any digitalisation effort.
And with that in mind, it is vital that we are developing people and creating a culture open to continuous improvements and change – a culture that has passion and self-drive.
To that end, as you look towards the future for Atlantic Grupa, are there any aspects to this culture that you’re still hoping for more improvement, or that are not as far along in their journeys?
I would say sustainability falls under this category. It should be part of any, overall development goals for sure. But unfortunately, we are still far from having completely sustainable operations.
Traditionally, operations and logistics are focused on speed and cost, while sustainable supply chain management includes the goals of environmental and societal values. We are becoming increasingly aware of this need and are slowly moving in that direction. For example, by increasing our fleet management efficiency, we are becoming more considered in how we deploy operational resources.
Meanwhile, we are at the end of a project which has seen us power our logistics operation in the main distribution centre via green energy sources. The road to sustainable operations in a very complex business environment is long, but steps are already being taken.
The future of the supply chain, and all its strands, is challenging and full of risk-taking decisions. But it is also full of new opportunities like this. I would say that letting go of old, traditional ways makes it more manageable to take advantage of such opportunities.
On the whole, it sounds like Atlantic Grupa is a forward-thinking, proactive company at a time of such drastic change. Is this how you would surmise the company’s identity, and its differentiating abilities in the market?
Atlantic Grupa prides itself on an ability to embrace, adopt and implement new innovations as part of a wider philosophy to continuously evolve.
By constantly improving our processes, looking for synergies in the system, and keeping pace with new trends and technologies, operations improvements can remain consistent with our corporate strategy.
Looking forward, it is essential to continue nurturing relationships with suppliers while retaining a customer-centric approach to leverage opportunities, and mitigate risks that are both near and far.